König Metall GmbH & Co. KG
Ingenics develops “quick wins” and long-term prospects
Reducing pressure to act, then generating “quick wins” and identifying new prospects
Following exceptional business performance, König Metall GmbH & Co. KG was under pressure to act. Among other things, logistical capacities were at their limit. In a short time, Ingenics consultants managed to identify areas of potential – transparency, process risks, and logistics efficiency – and to ensure a reduced workload through immediate measures while stimulating sustainable development. For König Metall, the result was a collection of quick wins and long-term prospects.
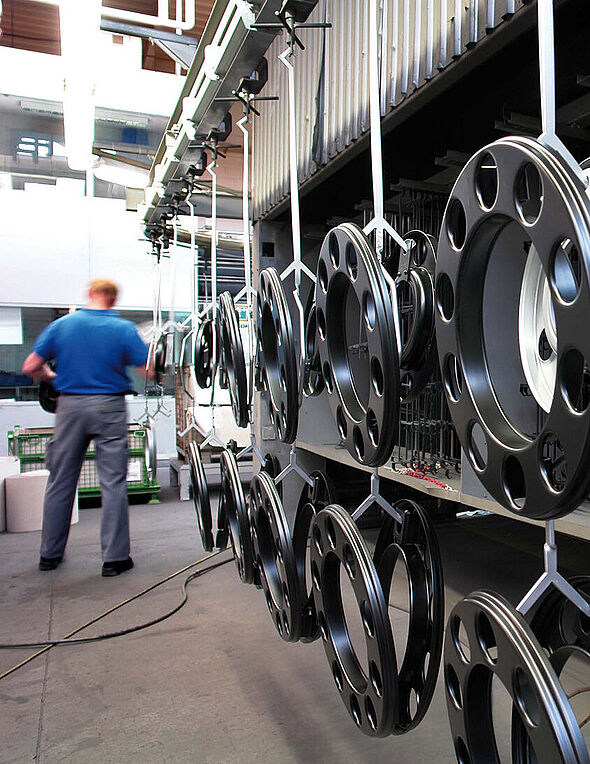
- Clarification of the need for action
- Identification of solutions for the short, medium and long term
- Realization of quick wins
- Ideal layout for expansion
- Development of target material flow
When production for a major customer was switched to König Metall, a new approach to production and logistics was necessary at the Gaggenau site. The management team began planning reorganization internally. A new, automated sheet metal storage system was procured and the installation site had already been agreed. Before any final decisions were made, however, it seemed necessary to draw on external experts to check and possibly optimize the proposed measures.
Ingenics’ consultants, entrusted with this task, quickly agreed with König Metall management that it would only be possible to overcome such challenging conditions with a tremendous level of motivation and commitment among all staff, including directors. As a first step, senior management expected a fast and thorough analysis of the entire material flow and logistics processes.
All areas of logistics and production processes were recorded in detail. When it came to analyzing material flows, every step of production was closely examined in addition to incoming and outgoing goods. Quantities transported by each carrier between steps was determined based on ERP system data. Standardizing volume of a transported unit per skeleton container made it possible to compare volume flows. Using a weighted material flow chart, this information was mapped to the plant layout, which revealed intersecting material flows and long transport distances between individual steps. The proposed production layout was confirmed to be a very good solution.
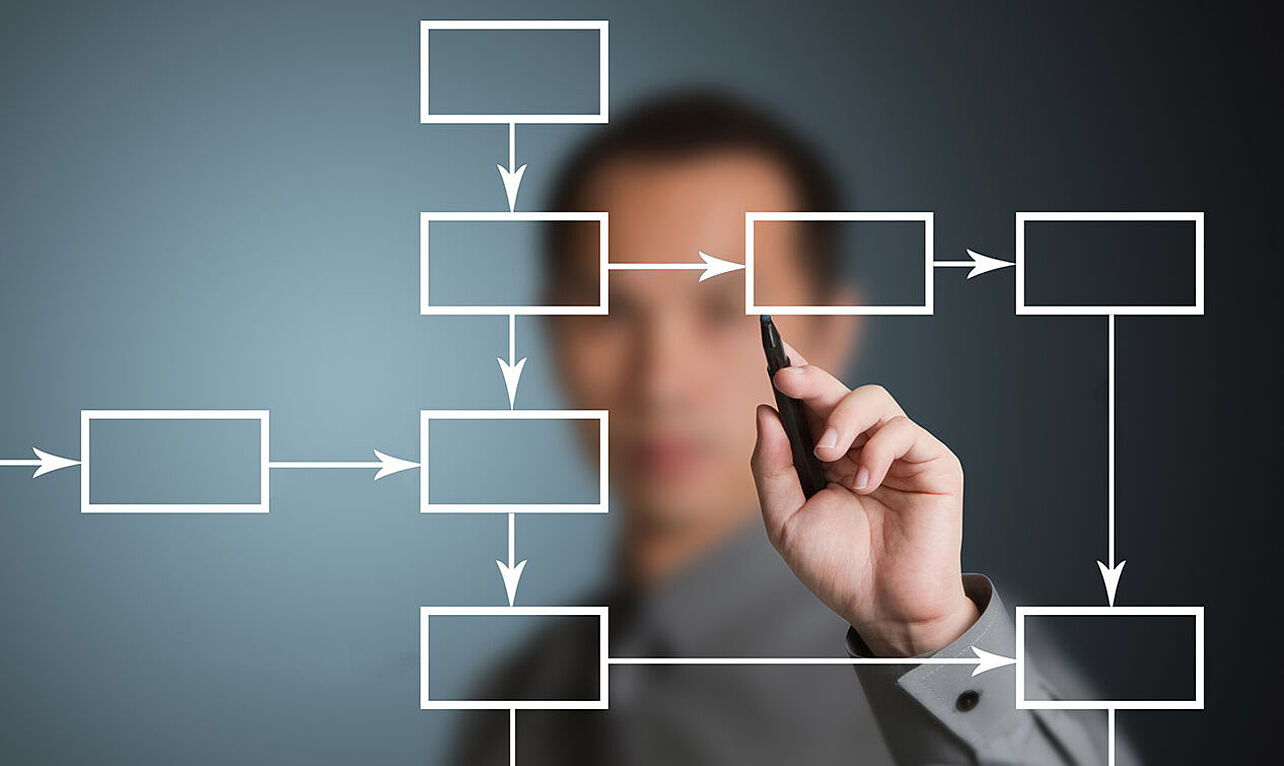
However, material flows were also identified that related to externally produced parts that did not necessarily have to be stored at the main plant. Given that storage technology had fallen short of requirements and capacity was being pushed to the limit, this meant unnecessary handling and severely limited flexibility.
Against this background, it was important to establish measures to reduce intense short term strain following a quick but thorough analysis while also developing concepts for long-term measures to ensure flexibility.
One result of the analysis was insight that it would make sense to outsource some logistical activities to external companies. Since storage is not a core competence of König Metall, transferring a range of tasks to logistics service providers had always been an option. Especially for parts that were only being handled at the main plant, it was essential to find a new solution.
Logistics related to actual production remained in the company’s own hands, but this was an area that had to be optimized with a transport control system and a direct ERP system connection.
With a focus on long-term, sustainable solutions, experts from Ingenics led strategy and layout workshops for management, production managers, and even the architect. Main topics of the strategy workshop were production space requirements resulting from projected business developments and identification of future capacity and space requirements in logistics and warehousing. The findings provided an immediate starting point for the ideal layout workshop, in which each functional area was arranged in line with the optimal flow of materials. All of this was then transferred to the actual layout and site plan. Importance was placed on the option of long-term, sustainable development within the company’s premises.
In this way, in response to positive pressure caused by excellent business performance, the project at König Metall to quickly identify areas of weakness – a lack of transparency, insufficient process reliability, and inefficient logistics processes – and to ensure an initial decrease in workload through immediate measures was ultimately a success.